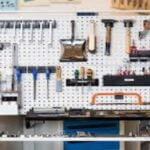
Maximizing Efficiency with 5S: A Guide to Creating a Visual and Standardized Workplace
July 18, 2022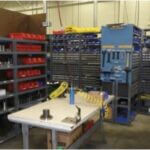
Mastering 5S: Key Strategies for Efficient and Sustainable Lean Implementation
July 18, 2022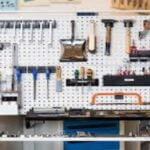
Maximizing Efficiency with 5S: A Guide to Creating a Visual and Standardized Workplace
July 18, 2022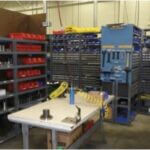
Mastering 5S: Key Strategies for Efficient and Sustainable Lean Implementation
July 18, 2022In the ever-evolving landscape of manufacturing, the adoption of the 5S methodology stands as a cornerstone for achieving a streamlined, efficient, and safe workspace. Originating from five Japanese terms that translate to sort, set in order, shine, standardize, and sustain, this approach not only fosters continuous improvement but also integrates seamlessly with lean manufacturing principles. The 5S methodology, a universal tactic celebrated worldwide, plays a pivotal role in enhancing manufacturing processes like just-in-time (JIT) production, cellular manufacturing, total quality management (TQM), and six sigma initiatives.
Understanding the 5S Methodology
- Sorting for Efficiency: The first step, sorting, involves identifying and eliminating unnecessary items from the workspace. This decluttering process sets the stage for improved efficiency and safety.
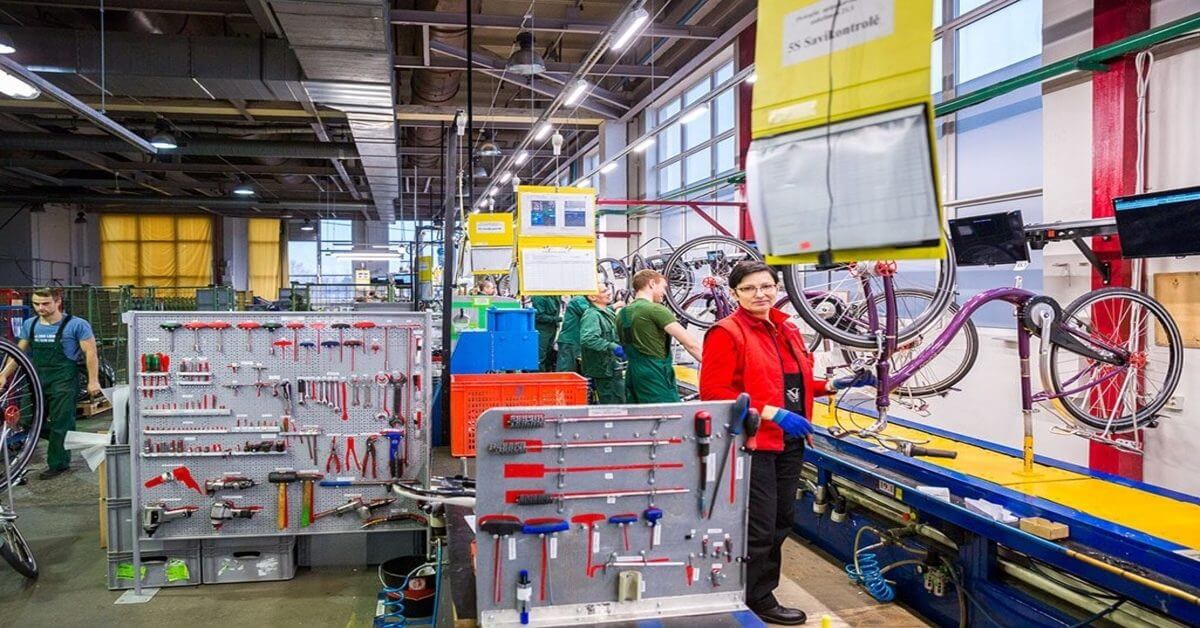
- Setting in Order for Organization: This phase focuses on organizing tools and materials logically, ensuring that everything has a designated place. This orderliness reduces time spent searching for items, directly impacting productivity.
- Shining for Maintenance: Regular cleaning and maintenance of the workspace prevent the accumulation of dirt and debris, which could lead to potential hazards.
- Standardizing for Consistency: Developing standardized procedures ensures that the first three steps are performed consistently and effectively across the entire organization.
- Sustaining for Continuous Improvement: The final step involves maintaining the standards and continuously seeking ways to improve them.
Enhancing Safety and Productivity A major benefit of implementing the 5S methodology is the significant enhancement of workplace safety. By organizing and standardizing processes, the chances of accidents and inefficiencies are drastically reduced. Additionally, 5S complements other safety initiatives, such as risk assessment and ergonomic improvements, making it an integral component of a holistic safety strategy in manufacturing.
Case Study: Streamlining Operations with 5S Consider the example of a factory plagued by wasteful practices, like excessive time spent searching for tools during changeovers. By applying the 5S principles, this time can be significantly reduced, enhancing both efficiency and safety. The method's versatility allows it to be adapted to various operational needs, making it a valuable tool for continuous improvement.
The 5S methodology transcends traditional organizational practices, embedding itself as a fundamental component of lean manufacturing. Its influence on enhancing safety, reducing waste, and fostering employee involvement is undeniable. By embracing this approach, manufacturing facilities can witness a transformation towards a more efficient, productive, and safe working environment. For personalized support in industrial safety products and expert advice in signage and workplace safety, turn to EZSecur. Discover more at www.ezsecur.com.